LU-YH-15-3.5-3 MAX Rubber recycling production line
Brand
|
LU-YH-15-3.5-3 MAX
|
Number of units
|
64
|
Name
|
1.Main attrition unit - 4 units |
Is not included in the set
|
all is included
|
Rated energy consumption
|
412 kW
|
Actual energy consumption
|
260 kW
|
Main engine power
|
43 kW
|
Water consumption
|
250 liters/day (cooling)
|
Raw materials consumption
|
12 000 kg/shift
|
Produces workpieces
|
12 000 kg/shift ( 10 delivery truck tires, 65 kg .hr)
|
Crumbs %
|
55% (0.5 - 1.0 mm)
|
Powder %
|
45% (0 - 0.5 mm)
|
textile
|
removes
|
Metal
|
Extracts
|
Recycles pure rubber
|
Recycles
|
Tires and bands containing textile
|
Recycles
|
Tires and bands containing textile and metal
|
Recycles
|
Tires containing metal
|
Recycles
|
Tires of diameter up to 4 m
|
Doesn't recycle
|
Productivity
|
Depends on rubber contents in raw materials
|
Productivity/shift
|
9 tons
|
- hr
|
0.9 ton
|
-shift (10 hrs)
|
9 000 kg/shift
|
- daily (22 hrs)
|
18 000 kg/day
|
- year (300 days)
|
5 400 tons
|
-metal scrap extracted/shift
|
Max -2 500 kg (depending on specifications of raw materials)
|
-Textile extracted/shift
|
Max -500 kg, depends on quality of raw materials
|
Raw materials consumption
|
6750 tons/year
|
Diameter of recycled tires
|
from 12 inches to 4.0 m
|
Operation mode
|
300 days/year, 22 hrs/day
|
Personnel, one shift
|
12
|
Skillful workers
|
3 persons
|
Shiftmen
|
8 persons
|
Foreman (engineer)
|
1
|
The shop is divided into sections. Number of Personnel for each section
|
2 sections
|
---Attritors section
|
5 persons
|
---Tires (up to 24 inches) preparation section
|
6 persons
|
Foreman (engineer) – total process control
|
1 person
|
Weight of the equipment
|
64 tons
|
Certification
|
Certified in Pr China, Vietnam, Mongolia, Ukrain, Kazakhstan, Egypt, Turkey, Czech, Israel, Russia
|
Factory warranty
|
1 year
|
Technical losses, %
|
0,001% of the raw materials weight
|
Production area without warehouses
|
1000 m2
|
It must be installed indoors
|
---Preparation section ---attrition section
|
Outdoor installation
|
Shredder can be installed outdoors
|
mounting
|
6 weeks
|
Fractions are controlled by replacement of sieves
|
8 fractions simultaneously
|
Foundation
|
Is required for main attritors - 3 units, 1 shredder
|
Factory start and adjustment specialists
|
Desirably, but not compulsory
|
Training of the personnel
|
Desirably but not compulsory
|
License
|
USA
|
Transportation
|
40 ft. containers – 5, 20 ft.container -1
|
Manufacturing time
|
60 days
|
Shipping time
|
66 days
|
Manufacturing time
|
90-120 days depending on destination
|
Spare parts
|
Are not included in the set.
|
Wearing parts
|
|
---abrasive shafts 8 units
|
Service time -2 years (made in Japan)
|
Circular blades-4 pcs | Service time - 1 year |
Chips crusher | Service time - 1 year |
---Blades of tire bead seat cutter
|
Service time -4 months
|
---Tire bead seat extruder's drums
|
Service time – 6 months (but it is possible to extend its service time and/or restore it
|
---Replaceable sieves
|
Time of service - 1 year
|
Manufacturing process
|
1.Removal of a tire bead seat >> 2.Separation of metal and rubber in tire bead seat >>3. Cutting of tire (without tire bead seat) in spiral bands of width of 3-5 cm >>4. Cutting off the second tire bead seat >> 5. Thinning of band >> 6. Cutting of workpieces >> 7. Production of powder and crumb >> 8. Separation into fractions >> 9. Removal of textile cord >> 10. Shredding of pure rubber (tread strips) and rubber containing textile cord >> Finished product warehouse |
The resultant products (powder and crumbs) are used to produce by further processing as follows
|
- raw reclaimed rubber
|
-mats for sport grounds of 500 х 500 mm
|
|
-filling seamless coatings
|
|
-Foam rubber
|
|
-Novotrack
|
|
-baseplates for rails and railway furniture
|
|
-Soles for slippers
|
|
- sanitaryware gaskets
|
|
- rugs for entrance doors and bathrooms
|
|
additives for asphalt
|
|
-Rubber blocks
|
|
-EPDM granules
|
|
-gasket and sealant for doors and windows
|
|
-Tread strips for restoration of tires
|
|
-Shock damper
|
Layout in the hangar 50*24*9 m
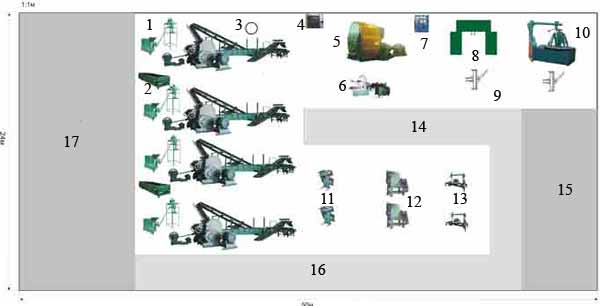
1. Air separator and final attritor
2. Supplementary fine polish screen
3. Cooling water tank
4. Control board
5. Shredder
6. Hydraulic shears
7. Metal extractor
8. Turtle
9. Hydraulic elevator up to 3 tons
10. Spider
11. Chips cutter
12. Band cutter
13. Cutter
14. Transport operatoin zone
15. Warm warehouse for raw materials
16. Transport operatoin zone
17. Finihed products warehouse